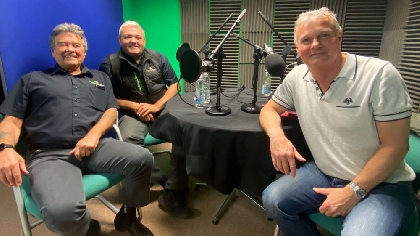
Podcast spotlights key players in the Tameside manufacturing chain
Dave Sweeton talks to the leaders, movers and shakers across the borough’s business world in our podcast series ‘Tameside Talks Business’. In the latest in the series, he turns the spotlight on manufacturing, featuring Tameside-based manufacturer Bestalinks Limited. Bestalinks is a precision engineering company, manufacturing mainly, although not solely, for the aerospace industry. A proud family-found firm, Dave is joined by Barry Smith and sons Martin and Stephen for the podcast. They explain the proud history behind the business and how it has continued to grow across a specialised market. This at a time when manufacturing as a whole across the nation has faced huge pressures and challenges, both historically and of course in more recent times, navigating the further problems presented by the pandemic, Brexit, plus the impact of the war in Ukraine and energy crisis. But Bestalinks has more than prevailed, rising above all those trials and tribulations locally, nationally and globally to continue to grow and diversify and meet tomorrow’s challenges today. You can hear the podcast in full on our social media channels.
You may be surprised to know that Tameside is the biggest manufacturing base, per head of population, within the Greater Manchester conurbation.
“As an engineer myself, it’s something I’m really proud of,” says ‘Tameside Talks Business’ podcast host David Sweeton.
But manufacturing across the country has, in his own words, faced troubled times.
“Engineering since the 1970s has not been in vogue. It needs to be, and training our own has never been more important,” he adds.
Bestalinks, a firm founded in the 1970s, has managed to forge ahead, successfully negotiating the troubled times of the past and present, to continue offering an engineering service that is technologically advanced and second-to-none.
In fact, although Bestalinks is associated with providing a service for the aerospace industry, its current remit is far more diverse and it was even involved in helping manufacture parts for early covid testing machinery.
It’s a remarkable achievement that a relatively small family firm in Tameside was able to play its part as everyone came together to take on one of the greatest challenges ever faced by humankind. And certainly not bad for a firm whose name was literally ‘plucked off the shelf for 50 quid’ back in the ‘70s.
Barry, Martin and Stephen Smith from the firm explain: “We worked all the way through Covid times, and we were fortunate that we could, as overnight the aerospace work stopped.”
Air travel of course was literally grounded globally as an entire mode of travel, let alone industry, came to a shuddering halt.
Bestalinks was able to undertake more work for the paper and tissue industries at the time (providing and servicing machinery used within the industry), meaning they could continue to operate through the pandemic.
But they also took on work to help indirectly to provide parts for covid testing machinery.
“With the Hyde Group of companies, they had covid testing machinery, and we helped out with those. They had a contract for that and subbed some of it to us. Everyone came together because they knew it was tough times, so everybody helped each other out,” explain the Bestalink team.
The remarkable covid link alone reinforces Dave’s declaration about just why engineering and manufacturing are so very important, not simply to the area, but the country as a whole, and why training young people in the industry is so vital.
It was all a far cry of course from the creation of the company more than 50 years earlier when the very notion of a global pandemic would have been more fiction than fact.
Barry shares how he founded the company with two other partners at the time, literally buying the name Bestalinks ‘off the shelf’ from a solicitor in London.
“It cost us £50 to set the company up,” he says.
Although associated today with supplying and serving the aerospace industry, the business back then was mainly involved in manufacturing parts for tools for the mining industry, securing key contracts from local manufacturers.
“We started doing work for the Hyde Group of companies and everything went well,” adds Barry, although he admits it wasn’t easy as they worked incredibly long hours, the partners initially juggling their own jobs to build up the business, sometimes working personally from eight in the morning until midnight.
But at the beginning of 1974, the business was fully up and operational.
These were tough times however in the engineering and manufacturing world.
Mining, the miners’ strikes of the ‘80s and demise of the industry, meant businesses Bestalinks supplied eventually ceased operating.
Recession saw other smaller businesses which had contracts with Bestalinks go to the wall, and Barry readily admits that as such businesses went bust, owing in some cases considerable sums of money to Bestalinks, so ‘they nearly took us with them a few times’.
However, due to the technical skills of the workforce they never had to chase work, and they eventually moved to undertaking contracts for the Royal Ordinance factory in Crewe (later BAE Systems) and hence the association with aerospace engineering began.
Bestalinks also undertook work for a textile firm in Oldham, providing a 24-7 machinery repair service.
It was in 1988 that the business became a family one, buying out the original partners, Barry’s sons joining later.
“My sons (Martin and Stephen) are in the business and the family dynamics are good,” says Barry.
“We don’t hunt for work and have a good reputation, so the work comes to us.”
Martin has worked in the aerospace, automotive and printing industries and Stephen in the aerospace industry before joining Bestalinks.
Both are time-served, fully trained engineers with the family team able to provide and offer experience across a range of industries, including aerospace, automotive, paper and tissue, plus food industries.
All share the importance of the businesses’ accreditation, for as an accredited company to BS EN ISO 9001:2000 standards, the family firm prides itself on being able to deliver complete sub-contract packages.
The team state: “We believe one of our greatest assets is our highly skilled workforce. With our continual investment in staff training and the latest in machine tool technology, we ensure that Bestalinks is at the forefront of the manufacturing industry in the North-West.”
They stress how closely they work with customers at all stages, ensuring all the project requirements are fulfilled with tight project control an essential feature, Martin overseeing sales and office work, with Stephen on the shop floor.
The business has recently relocated to a bigger site to accommodate its technologically advanced machinery, moving from Dukinfield to the Plantation Industrial Estate in Ashton.
The family share the move and all that it has entailed, plus exciting plans for the future and how the advances made in programming have themselves totally changed the engineering and manufacturing landscape.
It hasn’t all been easy though, and Barry, Martin and Stephen explain how Brexit has created real problems for all businesses, not simply their own, while the Ukraine war had a huge impact on the steel industry, sending prices literally ‘through the roof’ - ultimately price rises that have had to be passed on to the consumer.
The energy crisis too has had a similar impact and is leading the Bestalink team to explore introducing solar power and green energies.
Dave considers how manufacturing has shifted abroad with the team due to lower costs, but how some is returning and the importance of growing our own skills base and encouraging young people into the industry.
He highlights too the fantastic facilities available at Tameside College to train the next generation of engineers, adding there is a lot of money to be made in the manufacturing industry.
Bestalinks are now busy settling into their new Ashton base, where the future is looking bright and where seemingly work and family life appropriately live up to the business’ name.
“We’ve got the best of both worlds,” says Barry. “We enjoy our job and like working with the family.”